Understanding Vacuum Pressure Systems
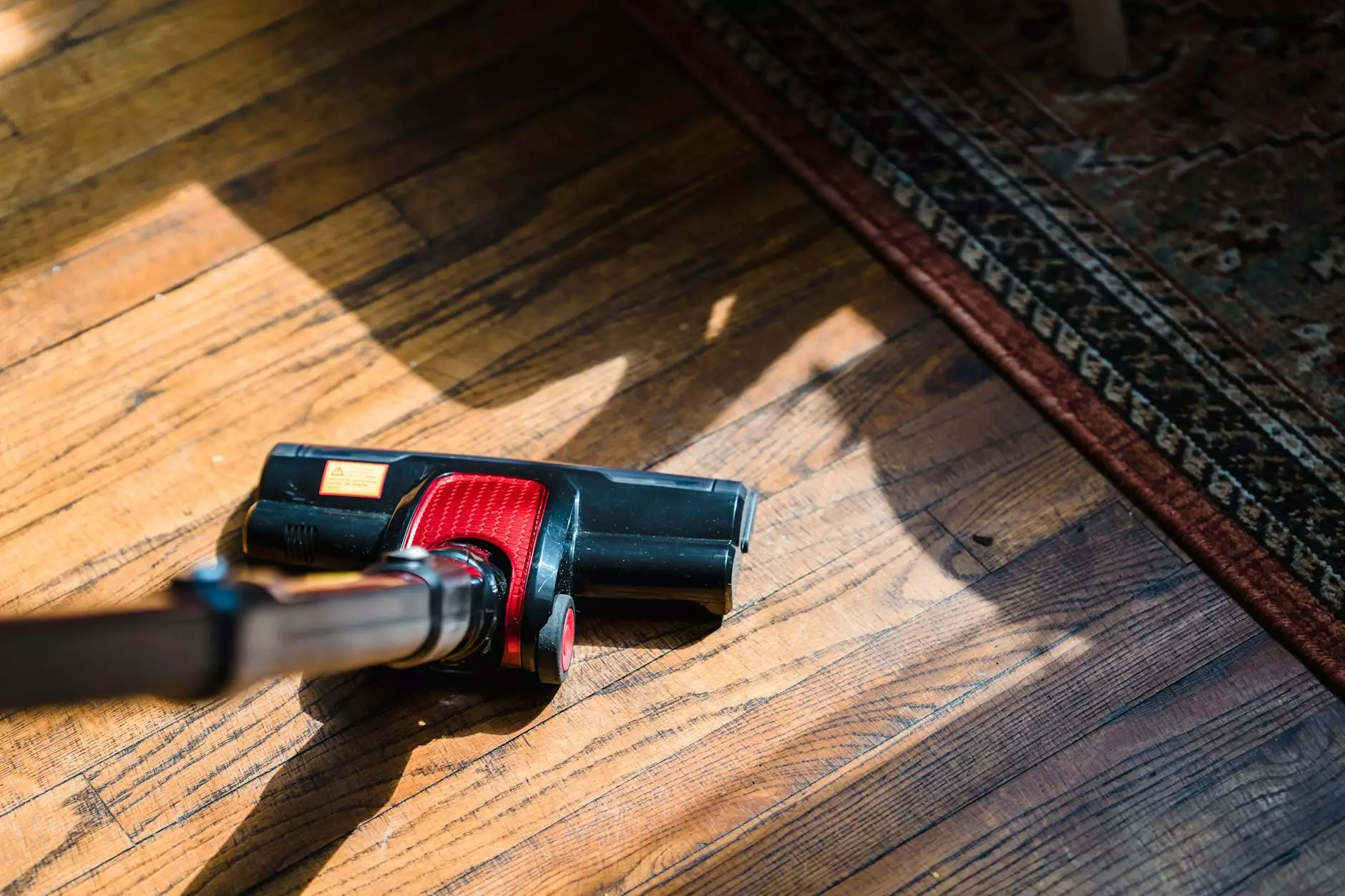
The Essence of Vacuum Pressure Systems
Vacuum pressure systems are critical components in various industrial applications. They operate by creating a vacuum that significantly reduces atmospheric pressure within a given space. This reduction in pressure serves numerous functions ranging from enhancing chemical reactions to facilitating the drying process in manufacturing environments.
How Do Vacuum Pressure Systems Work?
At the core of any vacuum pressure system is a vacuum pump. This device removes air and other gases from a sealed environment, thereby creating a vacuum. There are several types of vacuum pumps, including:
- Rotary Vane Pumps: Suitable for medium vacuum applications.
- Diaphragm Pumps: Excellent for low vacuum applications and fragile materials.
- Scroll Pumps: Known for their quiet operation and oil-free performance.
- Turbo Molecular Pumps: Used for ultra-high vacuum applications.
Each pump type has its unique function, making it essential to choose the right one based on the specific requirements of the application.
Applications of Vacuum Pressure Systems
Vacuum pressure systems find their place in a wide array of industries. Here are some of the most prominent applications:
- Food Packaging: Vacuum sealers preserve food by removing air to slow down spoilage.
- Pharmaceutical Manufacturing: In creating sterile environments for drug production.
- Vacuum Filtration: Employed in laboratories for separating solids from liquids.
- Electronics: Used in the production of semiconductors and circuit boards.
- Drying Processes: Industrial drying of materials like wood and textiles is enhanced by vacuum pressure.
Benefits of Using Vacuum Pressure Systems
Implementing a vacuum pressure system can provide numerous advantages for businesses. Some key benefits include:
- Improved Product Quality: By operating in a vacuum, reactions happen more efficiently, improving the end product's quality.
- Energy Savings: Vacuum processes often require less energy than conventional methods.
- Environmentally Friendly: Many vacuum systems decrease the need for chemical solvents, thereby reducing environmental impact.
- Versatility: Vacuum systems can be tailored to fit a variety of processes across different industries.
Common Challenges and Solutions in Vacuum Pressure Systems
While vacuum pressure systems present numerous advantages, they also come with challenges that need addressing:
1. Maintenance and Reliability
Regular maintenance is crucial to ensure system efficiency. Implementing a scheduled maintenance plan can minimize downtime and enhance reliability.
2. Ensuring Proper Seals
Maintaining vacuum integrity is critical. Regular inspections of seals and connections will help prevent air leaks and ensure optimal performance.
3. Choosing the Right Pump
Selecting the right vacuum pump based on application requirements is essential. Consulting with industry experts can help tailor solutions to specific needs.
The Future of Vacuum Pressure Systems
As technology advances, vacuum pressure systems are evolving. Innovations in materials, designs, and control systems promise to enhance the efficiency and application range of these systems.
Future trends may include increased automation in vacuum processes, resulting in more streamlined operations, greater accuracy, and minimized human error.
Conclusion
In summary, vacuum pressure systems play a vital role across various industries by enhancing processes, improving product quality, and promoting environmentally friendly practices. Understanding their workings and applications can lead businesses to integrate these efficient systems into their operations.
Discover More at TMM.COM.TR
For those interested in exploring high-quality services in the realm of Blow Dry/Out Services, visit tmm.com.tr to learn more about our offerings and how they can benefit your business.