Understanding Concrete Mixing Plants: Transforming the Construction Industry
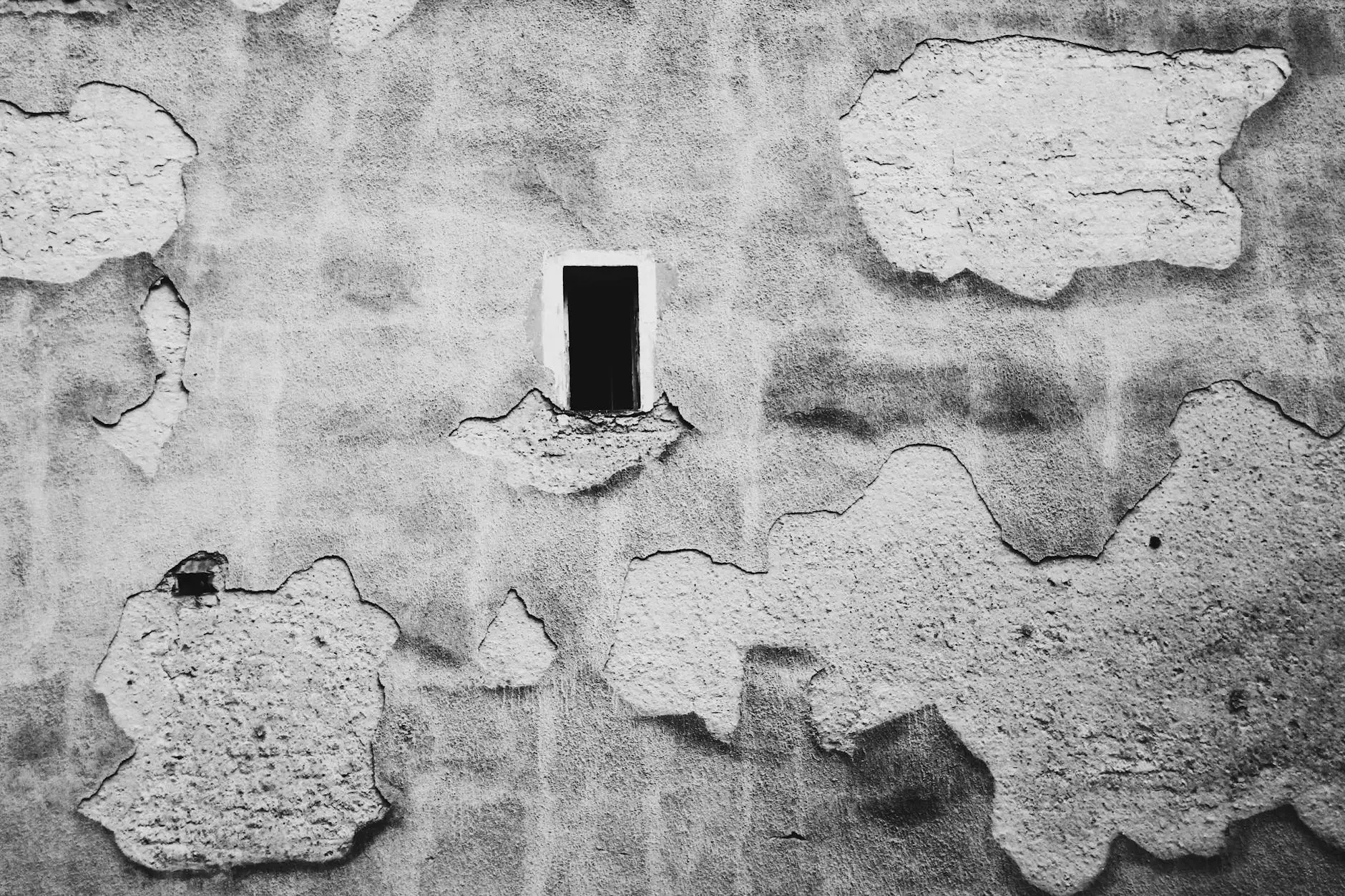
The construction industry is witnessing a remarkable transformation, driven by technological advancements and increased demand for efficiency. One of the pivotal elements in this evolution is the concrete mixing plant, a crucial facility that streamlines the production and delivery of concrete for various construction projects. This article delves into the intricacies of concrete mixing plants, exploring their functionality, advantages, and the pivotal role they play in modern construction.
What is a Concrete Mixing Plant?
A concrete mixing plant, also known as a batch plant or concrete batching plant, is an industrial facility that combines diverse components to produce concrete. These components typically include:
- Cement
- Aggregate (sand, gravel, crushed stone)
- Water
- Additives (to enhance properties, such as workability or curing time)
The primary function of a concrete mixing plant is to ensure that these ingredients are combined in precise ratios, resulting in high-quality concrete that meets specific engineering standards. Various types of concrete can be produced, including ready-mix, precast, and high-strength concrete, depending on the plant's configuration and equipment.
Types of Concrete Mixing Plants
Concrete mixing plants can be categorized based on several factors, including their production methodology, size, and mobility. Here are the main types:
1. Fixed Concrete Mixing Plants
Fixed concrete mixing plants are permanent installations often used for large-scale construction projects. They are capable of producing significant volumes of concrete and feature robust infrastructure designed for high output.
2. Mobile Concrete Mixing Plants
Mobile concrete mixing plants are portable units that can be easily transported to different job sites. They are ideal for smaller projects or locations where space is limited, providing flexibility and convenience without compromising quality.
3. Stationary Concrete Mixing Plants
Stationary concrete mixing plants are designed for long-term use on construction sites. They are set up for continuous production, making them suitable for large infrastructure projects where ongoing concrete supply is essential.
4. Compact Concrete Mixing Plants
Compact concrete mixing plants are smaller, more efficient setups that offer high productivity in a reduced footprint. These plants are ideal for urban environments where space is at a premium.
Components of a Concrete Mixing Plant
Understanding the specific components of a concrete mixing plant is crucial for grasping how they operate. Key components include:
- Batching Equipment: This includes scales and hoppers that accurately measure out the ingredients for each batch of concrete.
- Mixing Unit: The heart of the plant, where materials are combined to form concrete. It could be a drum mixer, pan mixer, or twin-shaft mixer.
- Control System: A sophisticated computerized system that manages the batching and mixing processes, ensuring precision and consistency in concrete production.
- Discharge Chute: The pathway through which the mixed concrete is discharged for transport to the construction site.
- Aggregate and Cement Silos: Storage facilities for the raw materials, ensuring they remain dry and uncontaminated prior to use.
The Benefits of Using Concrete Mixing Plants
Concrete mixing plants offer numerous advantages that enhance operational efficiency in construction projects:
1. Consistency and Quality
One of the standout benefits of concrete mixing plants is the ability to produce concrete with consistent quality. The precise measurements and controlled environment ensure that each batch meets the required specifications, ultimately resulting in stronger, longer-lasting structures.
2. Enhanced Productivity
With automation and streamlined processes, concrete mixing plants significantly increase productivity. They can produce large volumes of concrete in a shorter amount of time compared to manual mixing, aligning with tight project deadlines.
3. Cost Efficiency
By optimizing material use and minimizing waste, concrete mixing plants help lower overall project costs. Bulk buying materials and efficient mixing processes enhance profitability for construction companies.
4. Environmental Benefits
Modern concrete mixing plants are designed with environmental sustainability in mind. Many incorporate recycling systems for materials and water, contributing to reduced waste and lower carbon footprints.
Applications of Concrete Mixing Plants
The versatility of concrete mixing plants allows for their use in various applications across the construction sector:
- Residential Construction: High-quality concrete is essential for building homes, ensuring structural integrity and durability.
- Commercial Projects: From office buildings to shopping centers, concrete mixing plants provide the necessary materials for diverse commercial constructions.
- Infrastructure Development: Roads, bridges, and tunnels require large amounts of concrete, making concrete mixing plants critical in these projects.
- Precast Concrete Manufacturing: Many plants supply materials for precast concrete components, which are fabricated off-site before being assembled at the construction location.
Choosing the Right Concrete Mixing Plant
Selecting the appropriate concrete mixing plant involves considering several factors to meet specific project requirements:
1. Project Size and Scope
Assess the scale of your project to determine the capacity of the mixing plant needed. For large infrastructure projects, a fixed or stationary plant may be ideal, while smaller jobs might benefit from mobile solutions.
2. Type of Concrete Required
Different projects require different types of concrete, whether standard, high-performance, or special mixes. Understanding your demands will help in selecting a plant capable of producing the desired concrete mix.
3. Location and Accessibility
The location of your construction site plays an integral role in determining the plant's setup. Consider transportation logistics, space availability, and environmental impact.
4. Budget Considerations
Budget constraints are a significant factor in deciding on a concrete mixing plant. Weigh the initial investment against the potential long-term savings from increased productivity and reduced waste.
The Future of Concrete Mixing Plants
As technology continues to evolve, the future of concrete mixing plants looks promising. Innovations such as automation, artificial intelligence, and improved materials science are set to enhance plant efficiency, safety, and environmental impact. Here are some trends to watch:
1. Automation and Smart Technology
With the rise of smart technology, future concrete mixing plants will integrate advanced automation for real-time monitoring and adjustments, improving mix consistency and reducing human error.
2. Sustainable Practices
Environmental sustainability will remain at the forefront of concrete mixing plant innovations. Emphasis on using recycled materials, eco-friendly ingredients, and energy-efficient machinery will shape new plant designs.
3. Digitalization and Data Analytics
Data analytics can provide invaluable insights into production efficiency and material usage, allowing for informed decision-making and optimizing plant operations.
Conclusion
Concrete mixing plants are the lifeblood of the construction industry, delivering high-quality materials essential for creating robust, lasting structures. By understanding their operation, benefits, and future trends, businesses can harness the full potential of these plants, driving efficiency and enhancing the overall construction process.
Investing in the right concrete mixing plant from a reliable supplier, such as polygonmach.com, can lead to unparalleled success in today's competitive construction landscape. As technology advances and demands grow, staying informed and adaptable will be key to thriving in this dynamic industry.