The Essential Guide to Three Valve Manifolds for Efficient Fluid Management
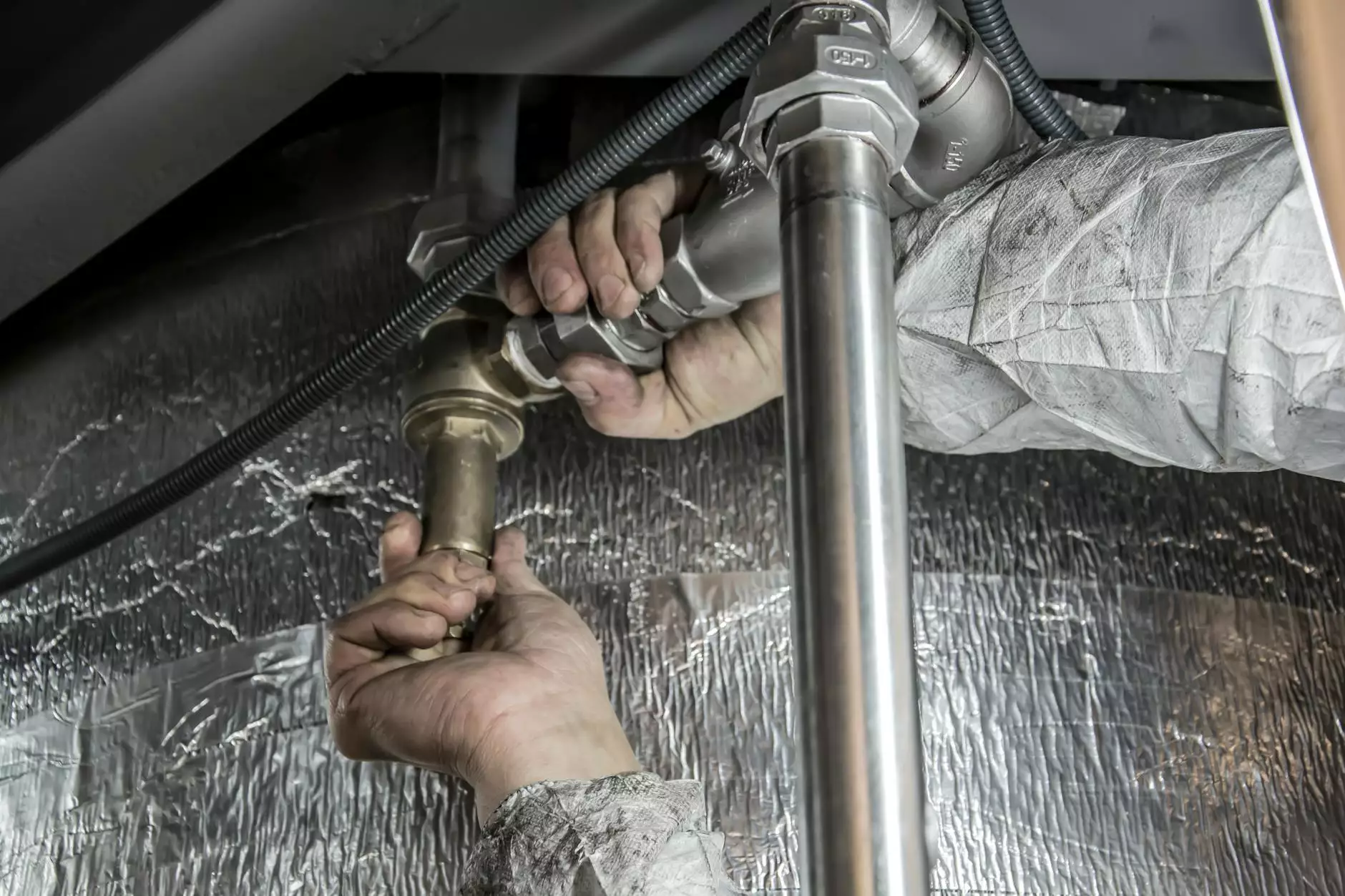
In an era where precision in fluid management is paramount, understanding the components and systems that facilitate seamless operations is crucial. Among the many devices designed for this purpose, the three valve manifold stands out as an essential tool for industries that rely on high-quality instrumentation. This article delves into the world of three valve manifolds, exploring their construction, applications, benefits, and their significance in modern business operations.
What is a Three Valve Manifold?
A three valve manifold is a specialized valve assembly predominantly used in the oil and gas, chemical, and instrumentation industries. Its primary function is to manage the flow of fluids through pressure and process instruments, providing a convenient connection between the process pipe and the measuring devices.
The three valves typically consist of:
- Blocks Valve: Control the flow of the fluid.
- Bleed Valve: Allow for the safe discharge of trapped pressure.
- Instrument Valve: Connects directly to the instrumentation.
Construction and Design of Three Valve Manifolds
The construction of a three valve manifold is a key factor in its performance and reliability. These manifolds are usually made from durable materials like stainless steel or brass, ensuring they can withstand high pressure and corrosive environments. The design often incorporates:
- Compact Design: Facilitates easier integration into existing systems.
- Robust Connections: Ensures tight seals and minimizes leaks.
- Instrumentation Compatibility: Works with a variety of pressure gauges and sensors.
Additionally, the design allows for easy maintenance and installation, providing flexibility in modifying or upgrading systems without significant downtime.
Applications of Three Valve Manifolds
The versatility of the three valve manifold makes it suitable for a wide range of applications. Businesses across different sectors can benefit from its use:
1. Oil and Gas Industry
In the oil and gas sector, three valve manifolds are indispensable for monitoring and controlling the flow of hydrocarbons. They provide critical data that assists in:
- Pressure monitoring.
- Flow measurement.
- System diagnostics.
2. Chemical Processing
Chemical plants utilize three valve manifolds to ensure safe operation in environments with potentially toxic or corrosive substances. They help maintain:
- Process integrity.
- Safety standards.
- Operational efficiency.
3. Water Treatment Facilities
In water treatment plants, the manifold assists in monitoring the quality and flow of water throughout the treatment process, contributing to:
- Improved water quality.
- Efficient resource management.
Benefits of Using Three Valve Manifolds
The adoption of three valve manifolds in fluid handling systems offers numerous benefits for businesses looking to enhance their operational efficiency:
1. Enhanced Safety
By providing safe pressure release and accurate flow measurement, three valve manifolds significantly reduce the risk of accidents related to over-pressurization and leaks.
2. Improved Measurement Accuracy
With their direct connection to instrumentation, these manifolds ensure highly accurate readings of pressure and flow rates, which are crucial for optimal system management.
3. Streamlined Maintenance
Three valve manifolds simplify the maintenance process. The isolation of instruments from the system flow allows for easy servicing without the need to shut down the entire system.
4. Cost Efficiency
While initial investments in high-quality manifolds may be substantial, the long-term savings from reduced downtime, fewer leaks, and enhanced operational efficiency can lead to significant cost reductions over time.
Choosing the Right Three Valve Manifold for Your Business
When selecting a three valve manifold, several key factors should be considered to ensure optimal performance:
1. Material Selection
Choose materials that match the corrosiveness and pressure conditions of your processes. Stainless steel is often preferred for its durability and resistance to corrosion.
2. Pressure Rating
Ensure that the manifold can handle the maximum pressure of your system. Overpressure can lead to catastrophic failures.
3. Connection Type
Verify that the manifold's connections are compatible with your existing piping and instrumentation systems to avoid installation issues.
4. Brand Reputation
Select manifolds from reputable manufacturers known for quality and reliability. A reputable brand can provide better support and warranty options.
Installation and Maintenance of Three Valve Manifolds
Proper installation and regular maintenance of three valve manifolds are crucial for ensuring their longevity and performance. Here are some essential tips:
Installation Best Practices
- Ensure all components are clean before installation to avoid contamination.
- Follow the manufacturer's guidelines for torque specifications and connection types.
- Test for leaks after installation using the recommended procedures to ensure a secure assembly.
Regular Maintenance Procedures
- Inspect seals and gaskets regularly for wear and tear.
- Conduct pressure tests to ensure the integrity of the manifold.
- Replace any damaged components promptly to prevent system failures.
Case Studies: Success Stories Using Three Valve Manifolds
Businesses across various sectors have successfully enhanced their operations by integrating three valve manifolds. Here are a few success stories:
1. Oil Refinery in Texas
An oil refinery implemented three valve manifolds in their pressure control system, which not only improved safety by reducing the risk of pressure build-up but also enhanced the accuracy of their measurements, leading to a 10% increase in efficiency.
2. Chemical Plant in Germany
A chemical manufacturer transitioned to three valve manifolds across their monitoring systems, resulting in a dramatic reduction in downtime for maintenance. The reliable structure of the manifolds provided greater operational confidence.
The Future of Fluid Management with Three Valve Manifolds
The demand for reliable and efficient fluid management systems is expected to grow, and innovations in technology will enhance the capabilities of three valve manifolds. Manufacturers are focusing on:
- Smart technology integration for real-time monitoring and diagnostics.
- Enhanced materials for increased durability and resistance to extreme conditions.
- Modular designs that allow for customization based on specific application requirements.
As industries evolve, so too will the designs and functionalities of three valve manifolds, ensuring they remain a critical component in efficient fluid management systems.
Conclusion
In conclusion, the three valve manifold is a vital instrument in fluid management, offering safe, efficient, and reliable operations across various industries. From the oil and gas sector to chemical processing and water treatment, their role cannot be overstated. By understanding their construction, application, and maintenance, businesses can leverage these tools to optimize their systems for improved performance and safety. As industries continue to innovate, the capabilities of three valve manifolds will undoubtedly expand, ensuring their relevance in the future of fluid management.
For more information about high-quality three valve manifolds and other fittings, visit techtubes.in, your trusted source for tube fittings, ferrule fittings, forged pipe fittings, and manifold valves.